安灯系统来源于丰田生产方式,是为了满足准时生产方式(JIT),让生产现场问题得到及时处理而安装的系统。有的工厂用灯光系统发问题信号,有的工厂用软件来模拟安灯,安灯的形式多种多样,而共同的目标都是用最直观的方式让生产现场的信息高效互通。除了在汽车行业中广泛使用外, 安灯系统凭借其实用性,近年来在很多行业都有安灯系统的身影。
经过了数十年的实践,安灯系统已经是一套经过广泛验证的成熟管理工具。但部署安灯系统导致的生产瘫痪不是一个小概率事件,而是许多工厂在开始生产现场管理改造时都遇到的挑战。羚数一家客户的CEO周总就遇到了这个问题。
“去年我们工厂来了一名精益专家,提出要用安灯系统来减少设备停机时长,提升生产效率和质量。但上了系统之后却发现各级管理人员很快被车间一线蜂拥而至的请求压垮,响应时间延迟,到最后操作员也放弃了求助,改造宣告失败。”
其实,实施安灯系统的困难并不在于安灯本身,而是在于应对安灯信号的能力问题。对于刚开始进行数字化管理改造的企业来说,问题不在于你是否应该使用安灯,而是搞清楚你需要做哪些工作才能让安灯更好地发挥作用。
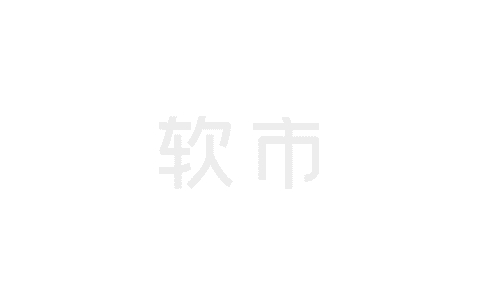
安灯系统越用生产现场越混乱,症结在哪/strong>
安灯系统的作用是为了尽快暴露影响生产的问题,如果没有安灯系统,这些问题可能会被忽视,从而导致更严重的生产事故。这就是为什么用了安灯系统之后,暴露的问题确实越来越多,但团队反而应对无措。小羚总结了以下的一些常见的原因:
问题没有分级分类描述与升级机制,响应人员毫无准备
生产员工在使用一些相对传统的安灯系统时,由于缺少问题分类的功能,导致不论是什么问题,统统上报。收到通知的响应人员,只有到了现场才能知道问题的类型,如果不是他职责(能力)范围内的问题,又需要再通过电话、微信等通知相应的专业人员来处理。一来二去处理的时间就被严重拉长。
通知效率低,响应人员到位不及时
尽管许多的安灯系统能第一时间把问题的定位和严重程度显示在车间现场大屏上,但由于没有和当日在班的响应人员的联系方式(电话、短信)绑定,导致响应人员接收通知滞后甚至错失,同样会造成问题响应的不及时。
问题解决进度没有持续追踪,一波未平一波又起
在使用安灯系统的前期,车间里每天都会出现数十次甚至上百次异常警报。有的响应人员可能每天都会疲于四处解决问题,却忽略了每个问题是否彻底解决。对于管理者来说,只是看到了各个角落都在上报问题,却无法知道现场问题的处理进度和方案,对于生产进度和节拍的影响就很难估算。
高频、复发问题难以积累解决方案,小问题大折腾
就像周总的工厂一样,一线人员只要遇到问题就会使用安灯系统。即便是已经处理过的小问题也会反复上报,问题数量始终难以降低。如果没有针对常见问题的快速解决方式和经验沉淀,安灯系统就不能达到优化响应速度、提升管理效率的最终目标。
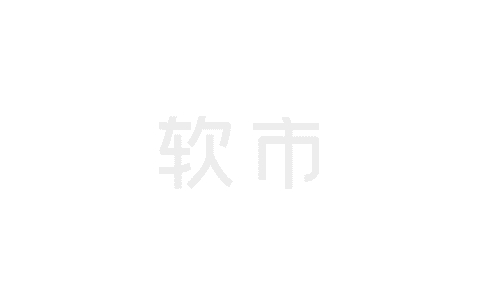
安灯系统想用好,生产管理体系必不可少
小羚告诉周总,安灯系统包括其他的各类数字化执行类软件、系统都不能直接解决工厂的生产管理问题。因为问题的关键永远是工厂内部的生产运营管理体系,它解决的是人和人、人和机器之间的合作效率瓶颈。
因此想要把安灯系统用好,管理者首先要做的是梳理管理流程,根据工厂内常见的设备、原料、安全、人员等不同部门确定响应人员的分工、职责、权限、执行标准等规范,形成标准化响应机制。
根据问题影响时长等严重程度指标,设定问题升级规则,通知高层管理人员注意,并在工厂的异常管理目视化看板中持续显示。最终工厂管理人员能够根据异常发生的数据,发现要去改善的环节,从而逐渐减少问题重复发生的频次。
羚号工厂生产运营管理系统安灯看板
同时我们需要定义关键节点的指标体系:包括但不限于平均响应时间、平均处理时间、有多少问题是等待关闭,等待响应、以及每个问题的执行进度,提升现场生产问题的透明化、紧迫感。提升人员执行力和解决问题的能力,才是使用安灯系统的最终目标。
通过持续的运营管理策略优化,不断提升管理基础,才能让工厂的生产效率实现数十年持续稳定提升。
来源:羚号工厂
声明:本站部分文章及图片转载于互联网,内容版权归原作者所有,如本站任何资料有侵权请您尽早请联系jinwei@zod.com.cn进行处理,非常感谢!