O 引言
质量功 能展 开 (QualityFunctionDeployment,简 称QFD)是产 品设计阶段的一种工具 ,其实质是用一种系统工程的观点将顾客的需求转化为工程特性。传统的QFD过分的强调顾客的需求 ,但是 由于顾客需求 的可变性及通过四个阶段 的转换 又极有 可能被扭 曲,所 以顾客需求并不能真正得到反应 ;同时 ,在质量屋中,一些序列性 的数字(如 1、3、9等)无法准确的反映出技术要求之间,以及顾客需求和技术要求之间的复杂关 系。失效模式及影响分析(FailureModesandEffectsAnaly—sis,简称 FMEA)找出过程 中潜在的质量问题或失效模式 ,分析所造成影响的严重性 ,发生频率及现有控制手段所能检 出的难易程度 ,以便及 时采取有效 的措施。但是 ,FMEA也是一 项繁琐 ,极耗时间的过程,对失效模式 的列举本身就是应用头脑风暴法 的一个过程 ,靠的是一种抽象 的思维及对以往经验 的总结 ,因此 ,对一种失效模式的遗漏可能造成难以弥补的后果。如果将QFD与FMEA进行整合 ,建立一个集 成模型 ,把 四类FMEA嵌入到 QFD四阶段模型当中,将有助 于消除二者应用的局限性 ,从而减少产品设计次数的重复 ,及 时发觉潜在的设计缺陷 ,收到 良好的效果。
1 QFD与 FMEA 的集成理论
1.1 质量功 能展 开
QFD的创始人 AkaoYoji…将其定义为“将顾客 的需求质量转换成质量特性 ,决定产品的设计质量 ,在各功能部件的质量 ,甚至每个零件 的质量及工序 因素之间,一边表明它们 的相互关系 ,一边 系统地展开”。其核心工具是质量屋——一种直观的矩 阵展开框架 ,其包括顾客需求 ,工程特性 ,相关矩阵 ,关系矩阵 ,计划矩阵 ,技术竞争性评价六个基本部分。随着 QFD方法的不断完善 ,它的应用也从最初 的汽车制造业扩展 到了整个制造行业 ,以及后来 的医疗健康 、软件开发 、交通运输和教育 等行业或部 门。目前较为流行的质量功能展开的模式是美 国供应商 (ASI)协会的四阶段模式 ,即为将顾 客需求 转化为设计 要求 ,零 部件要求 ,工序要求 ,生产要求 四个阶段。
1.2 失效模式及影响分析
FMEA是使用系统分析 的方法对产 品设计 ,开发 ,制造等过程进行有效 的分析 ,找出过程 中潜在 的质量问题或失效模式,分析所造成影响的严重性 ,发生频率及现有控制手段所能检 出的难易程度 ,以便及时采取有效的措施,最大限度地减少或避免质量损失,降低质量成本 ,提高效率。
关于 FMEA,有如下 四种分类 :
系统 FMEA——用于在早期构思设计 阶段分析系统和子系统,系统 FMEA着重分析 由系统缺陷引起的与系统功能相联系的潜在失效模式 ,它包括对一个系统与其他系统间的相互作用以及系统的单元 间的相互作用的分析 ;设计 FMEA——用 来在产品交付生产 前分析产品 ,重点分析由设计缺陷引起 的产品潜在失效模式 ;过程 FMEA——用来分析制造或装配过程 ,重点分析由制造或装配过 程缺 陷引起 的潜在产 品失效模式 ;服务 FMEA——用于在服务 到达顾 客前对服务进行分析。
1.3 QFD与 FMEA的相似性与互补性
二者还存在着很多的相似点
QFD和 FMEA的最终 目的都是为了质量的持续改进 ,提高顾客满意度。
QFD的本质就是基于并行工程 的思想 ,强调跨职能团队的合作 ;而设计 FMEA作为一种可靠性设计方法,其主要 目的就是为保障与改进设计提供相关的依据,这 同样也是一种并行设计 的思想 ,因此 ,二者在本质上是一致的。从根本上来说 ,在一个集成 的质量管理系统中,二者可以共享一个数据库 ,以实现最底层数据信息的共享与集成。
同时,二者也 有一些差别 ,并且 二者 如果 单独使用 ,存在着很大的局限性 ,因此 ,从功能的角度而言,二者存在着很大的互补性 :
从两种质量工具的出发点来看 ,虽然最终 目的都是顾客满意,但是 QFD从 正面的角度 出发 ,通过对产品特性的一层层展开、与竞争对手的基准评价来达到客户需求 ;而 FMEA则换了一个角度 ,从预防产品或过程失效的方式 ,来 消除顾 客可能产生 的不满。传统 的QFD过分的强调顾客 的需求 ,但是 由于顾 客需求 的可变性及通过 四个 阶段 的转换又极有可能被扭 曲,所 以顾客需求并不能真正得到反应 ;同时 ,一些序列性 的数字 (如 1、3、9等)无法准确 的反映出工程特性之间,以及顾客需求 和工程特性之间 的复杂关系。因此 ,QFD与其它质量改进方法或数学工具的集成成为一种必然的发展趋势。而 FMEA则恰好可 以消除传统 QFD的一 些局 限性 :
(1)尽管顾客需求可能会发生改变,但对各功能单元其失效的模式及原 因一般不会有大 的变动,通过分析发生失效的原因是 由哪些工程特性没有满足所造成的,可以达到:在顾客需求发生变化的情况下 ,使 相应的工程特性不会有大 的变动,达到“万变不离其宗”的目的,因此消除由于顾客需求变化所造成的障碍 。
(2)通过设计 FMEA对各个功能单元失效模式及原因的分析可以减少由于序列性数字对相关性矩阵评价所造成的影 响。具 体说来 ,QFD的第二阶段是将工程特性展开为零部件特性的阶段 ,是将整个产品展开为零件的一个分解过程 ,因此评价零部件特性之 间的关系时容易孤 立的考虑 ,造成误差 。FMEA在分析 失效模式时需要考虑破坏零部件之 间的连接这样一种失效模式 ,这本身就是一个将零部件结合成整体的过程 ,
因此,可以将信息反馈到 QFD中,有助于对相关性矩阵的评分 。FMEA的结果可以用于重新评价 QFD中的质量屋(HOQ)和质量计划中的 目标值。FMEA可 以消 除 QFD 的一 些 局 限性 ,反 之 ,QFD也可以帮助 FMEA克服一些障碍 ,这是因为 :
1)FMEA也是一项繁琐 ,极耗时间的过程 ,对失效模式的列举本身就是应用头脑风暴 法的一个过程 ,靠的是一种抽象的思维及对以往经验 的总结 ,因此 ,对一种失效模式的遗漏可能造成难 以弥补的后果 。但是通过 QFD的逐级展开,不断细化 ,分解的过程 ,可以确保FMEA尽可能详尽的列举出大量关键 的失效模式。
2)在系统 FMEA之前可进行 QFD,结果对于跨职能设计开发小组在 FMEA分析中有如下帮助 :
①确定关键的质量特性 ;
②分析产品的可靠性和安全性与工艺特征间的关系 ;
③分析失效 模式 的严重 度和顾 客需求之 间的关系 ;
④使系统 FMEA的开展有一个整体的视野 ;
⑤减少在评价故障的严重性(s)、发生可能性 (O)和可检出性 (D)中的主观偏差。
2 QFD与 FMEA的集成模 型
在产 品的设计和开发 阶段 ,两者都是系统化 的分析工具。从所涵盖的设计 阶段来说 ,质量功能展开 四阶段模型始于客户的需求 ,止于对生产制造过程 的详细设计 ,而四类 FMEA始于对产品概念设计 的失效分析 ,止于对产 品到达顾客手 中之前 的服务失效 分析。
两种工具在产 品和过程 的设计 阶段 中有大部分 的交叉 ,而不同的部分又有相互补充的内涵,构成 了一个完整的产品开发过程 。具体来看 ,在质量功能展开第一阶段之后可 以进行系统 FMEA,用于对产品的系统 和初 步设计进行质量评估 ;而设计 FMEA用于在质量功 能展开进行到第二阶段 后 对产 品 的 详 细设 计 进 行 设 计 评 审;过 程FMEA在质量功能展开进行 到第三阶段后对产品的加工装配过程进行评审 ;服务 FMEA则用在质量功能展开完成四阶段之后对产品在交付顾客使用之前对服务进行最后的分析。应该指 出,在每一个 阶段 ,FMEA对QFD的分析结果仍然具 有反馈 的作用 ,QFD的结果应该在 FMEA的基础上进行修改和完善,见图 1所示 。
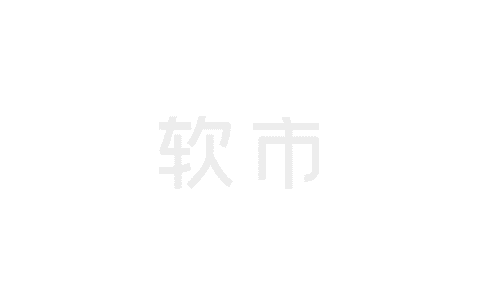
图 1 QFD与 FMEA集成模型
3 应 用实例
As型 电动葫芦 由驱动制动装置电动机、传动装置减速器、取物缠绕装置 (吊钩、卷筒等)和电控部分组成 ,在组成电动葫芦的几个部件 中,电动机 、减速器 、控制箱都可按标准的型号 和规格通过外购获得 ,只有取物缠绕装置 ,必须根据用户订货要求 的起升高度一一订制。因此 ,取物缠绕装置是电动葫 芦的整机生产厂家必须保留的自制部件 ,是成功企业的核心竞争优势 ,结构图如图 2所示。
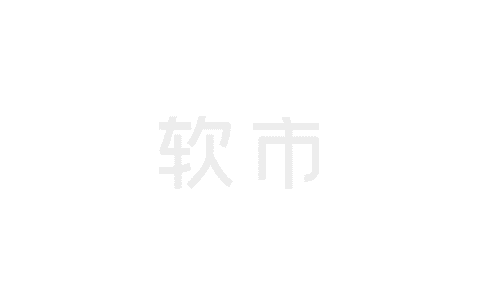
本文就 AS型电动葫芦利用 自己开发的集成软件进行 QFD展开 ,并在第二阶段之后进行设计 FMEA分析,以体现 QFD与 FMEA的集成 思想 ,软件界面上着重体现 QFD与设计 FMEA的结合 。取物缠绕装置的设计 和制造对起重量 、起升高度和起升速度这三个参数都有重要的影响。QFD展开 的第一阶段如图 3所示 。
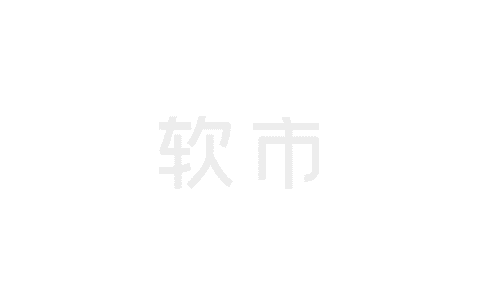
在经过 QFD第一阶段的分析之后 发现对 电动葫芦的主要客户需求均体现在取物缠绕装置的卷筒 的可靠性与安全性上 ,由此应进一步进行系统 FMEA,对取物缠绕装置进行初步设计 ,并考虑取 物缠绕装置 与其它三部分之间的相互联系及影响 ,其输出为 QFD第二阶段 的输入。QFD的第二个阶段将工程特性展开为具体的套筒 ,支架 的零部件特性 ,进行设计 FMEA,进一步分析各个零部件可能产 生的潜在失 效模式 。设 计FMEA总表见图 4所示。
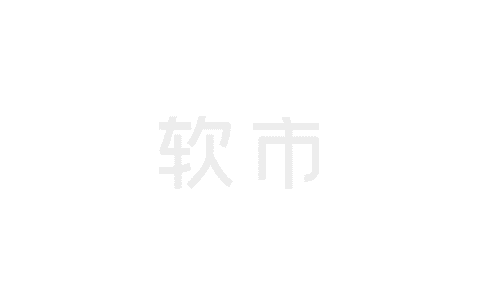
图 4 设 计 FMEA总 表
由于第二个阶段的 QFD的展开 ,保证设 计 FMEA尽可能详尽的列举出了幅板和套筒脱落 ,端盖断裂 ,端盖焊缝裂纹 ,支架与减速 器松动突 出这样 四个关键的失效模式。从设计 FMEA计算 的 RPN的结果 可以看出,支架的 RPN一般 均高 于套筒 的 RPN,所 以,设 计FMEA对 QFD第二阶段提供 了反馈 ,支架的重要程度是高于套筒 的,于是 ,在 QFD的第二 阶段 当中通 过调整相关矩阵的相关度 、关 系矩阵 的关系度 以及计 划矩阵,使支架的重要程度高于套筒。
QFD的第三阶段将零部件特性转化为加工过程分别是焊接和车幅板外 圆,然后继续做过程 FMEA,对 制造加工装配过程评审 ,同理 ,过程 FMEA也对 QFD第三阶段提供反馈。QFD的第四阶段将过程转化为具体的一些操作 ,分别为电压 、电流、焊接速度 、焊接角度 、车床 轴 线 跳 动 以 及 车 床 同心 度。最 后 进 行 服 务FMEA,在取物缠绕装置成品进人下一阶段 的装配之前对服务作最后的分析。
QFD的第二、三、四阶段界面可以参考文献 (何桢,邹峰,赵燕.基于 QFD质量工具集成研究与应用.组合机床及 自动化加工技术,2006,1:96—99,102])。
在上例中,QFD与 FMEA集成使用 ,避免了 FMEA中失效模式 的遗漏 ,FMEA又对 QFD第二阶段中零部件特性的重要度反馈修改 ,因此可以提 高产 品的设计质量 ,降低产品的设计周期与成本。
4 结束语
由于 QFD和 FMEA各 自存在着局限性 ,但是二者又存 在 着 相 似 性 ,因 此 ,将 二 者 集 成 使 用 ,将 四类FMEA嵌入到 QFD四阶段模 型当中,是可行 的,同时 ,能够互相弥补各 自的缺陷 ,利用 QFD与 FMEA集成软件对 As型电动葫芦所做的集成应用研究表明将 QFD和 FMEA集成对企业提高设计质量 的重要作用。
来源:聪脉(上海)信息技术有限公司
声明:本站部分文章及图片转载于互联网,内容版权归原作者所有,如本站任何资料有侵权请您尽早请联系jinwei@zod.com.cn进行处理,非常感谢!