本期导读:
随着当前智能制造战略和IoT驱动的技术创新浪潮,制造设备将会变得越来越智能。未来的网络技术将会使得机器、设备、传感器、RFID标签、机器人和自动化控制器实现互联互通。未来的“智能”工厂有望达到一种全新的协作水平,呈现出过去认为不可能实现的效率与敏捷性。
这套技术被称为“工业物联网”(IIoT),属于“物联网”(IoT)的一个分支。在工业化国家中,一场改变商品生产与服务管理方式的转型已经启动。预计转型将带来革命性成果。媒体舆论中充斥着各种关于新技术的信息,但是关于业务流程转型机制的内容却比较罕见。
数字化技术的最新发展,包括大数据分析、云应用、业务流程管理(BPM)、社交媒体、IIoT和流动性等,促成了“拉”的影响超越精益制造的范畴。鉴于这些科技新发展,其中可以归结为两大动力:拉动力和数字化动力。本文通过实际应用的介绍,展示勇于创新的制造商如何更好地利用数字技术来实现卓越运营的新水平。达索系统将这些力量的协同效应称作“智能拉。”
“拉”流程机制——由单个真实事件触发(相对于通过预测触发),已经不是新事物。它早已成为许多成功制造战略的核心。约翰·哈格尔三世、约翰·西利·布朗和郎戴维森合著有《拉动力》一书。书中提到拉动力指的是不唯一依赖规划或预测,拟定出所需人员与资源来积极应对挑战并妥善把握好机遇的能力。
拉流程是由真实事件触发的业务流程。与此相反,推送流程是通过进度规划或预测触发的。
拉并不是完全摆脱预测。虽然拉流程的执行是由真实事件触发的,但是拉流程的顺利实施往往依赖可靠的预测和规划结果。例如,生产均衡和排序都属于规划技巧,用于确保看板流程的顺利运行。在其他情况下,制造资源的分配可能在规划级进行,而执行的时机则由拉确定。设计均衡的推拉流程运营模式为制造商带来了不断演进的挑战。
当事件发生时,拉流程能够执行相应措施来补偿预测产生的误差,从而形成一一个优于推主导方式的执行路线。
拉流程是实现高效大规模定制的关键所在。虽然大规模定制这个术语已经面世几十年,新的智能拉流程可将大规模定制提升到新水平。下面是基于拉的三个主要大规模定制类型。
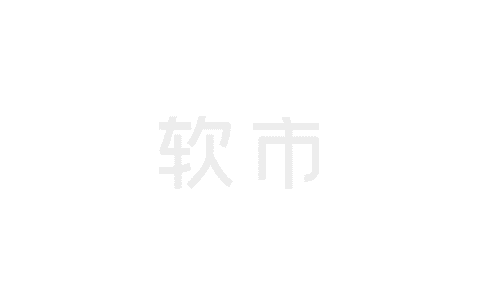
智能拉提供的大规模定制的类型。
据说,丰田花了十几年的时间,才使他们的看板拉动系统成功工作。在生产流程中成功应用拉之前,丰田形成了精益文化,成功落实快速换模法(SMED),生产水平制度化,建立起一个连续的生产流程。虽然这些因素对于实现长期成功非常重要,今天的智能拉解决方案可显著缩短拉执行的价值实现时间。
下面我们来看一个实际案例:汽车业供应商在装配过程中对MTO和MTS进行混合
汽车业供应商必须根据OEM装配线的特定序列为汽车OEM客户供货。而其他人通过堆放成品库存,然后基于序列发货,以满足这一需求,这家汽车座椅制造商通过转型到基于序列制造的模式而大幅减少库存。这种进步的一个关键因素是应用了智能拉解决方案,不仅有助于最终成品的装配,也可对根据序列提供的半成品进行制造。在同一条生产线上,当存在额外的产能时,生产黑色座椅采用的是MTS,而对于其他所有特殊颜色座椅,执行的则是MTO。
- 使用拉来改善推标准数据的准确性——在可通过拉改善的ERP和调度系统中,标准生产周期、成本和容量参数是典型的主数据实例。来自标准计划数量的实际数据中的任何显著偏差都可以配置为自动更新,可对这样的主数据进行自动更新。
- 使用拉简化计划和订单管理——业界通常用规划和调度系统来确定成千上万订单的开始和结束时间,不仅包括生产和物料转移订单,同时也包括维护、检查以及其他类型的订单。使用智能拉可以简化这个任务。拉可使操作产生流动,而不是强制启动与结束这些大量订单。管理者应该监控更多有意义的操作参数,例如:吞吐量、产能、WIP级别以及拉触发点。这些是流量所依赖的参数,因此管理者无需对成千上万任务和命令细节调度进行管理,从而更妥善控制流量。
智能制造和工业物联网领域多数报道专注于阐述高级硬件设备的应用,例如智能传感器、机器人系统和自动化设备等。在本案例中,我们提出了一个强调数字化和业务转型的框架,这在许多情况下不依赖于高级的自动化,并且在大多数情况下都更加重要。这样的企业转型基于信息流的新机制,现在借助“智能拉”成为了可能。
采纳上述“智能拉”的概念将大有裨益,可以将注意力从技术上转移到业务转型上。然后,基于推的挑战和效率低下问题将化身为机遇。或许您可以通过提出以下问题来找出存在机遇的领域。
- 哪种资本封锁或等待时间改善对您的业务影响最大?
- 能否使用拉改善这些领域?
- 哪个客户参与度或操作效率低下的部分可以通过将推改为拉予以解决?
“智能拉”概念确实具有革命性,因为它能够助力将这些业务转型成果投放市场。
来源:网络转载
声明:本站部分文章及图片转载于互联网,内容版权归原作者所有,如本站任何资料有侵权请您尽早请联系jinwei@zod.com.cn进行处理,非常感谢!