江苏激光联盟导读:
本文介绍了钠、石灰、硅玻璃的激光粉床熔接。
玻璃具有许多吸引人的特性,如透明度、耐化学性、良好的热稳定性和高电阻率,使其成为一系列应用的有利材料,包括医疗技术、电子、化学和制药行业。然而,与金属和聚合物相比,玻璃的增材制造仍处于初级阶段。玻璃固有的材料特性,即其非晶态结构,缺乏延展性和较高的加工温度,使添加剂制造玻璃的加工具有挑战性。本文介绍了钠、石灰、硅玻璃的激光粉床熔接。激光粉床熔合工艺进行了优化,制造出的零件的物理和机械性能特征显示,平均孔隙率为12%,平均抗弯强度为6.5?MPa,为全非晶结构。通过实例验证了其可行性,表明复杂几何形状是有可能实现的。即使制造的部件是不透明的,它们也可能在化学和制药行业对化学惰性和几何复杂性的需求超过对透明度的需求的应用中找到应用,例如连续流反应器或结构化催化剂。
1. 介绍
玻璃由天然和丰富的原材料制成,具有独特的物理性能,包括透光性、透明度、化学耐久性(腐蚀性溶液是常见的例外)、热稳定性和电阻率。这些特性使玻璃吸引了从建筑、汽车和航空航天工业到电子、包装、化学制造和制药行业的广泛行业。目前,复杂形状的玻璃创建使用模具如在玻璃铸造和紧迫或玻璃热弯,通常用于建筑或汽车行业,在平板玻璃加热高于其转变温度,重力将模具下玻璃的形状。不同的玻璃几何形状需要单独的模具,这增加了成本,并在这些生产过程中嵌入碳。激光烧蚀或微加工等减法方法被用于化学制造、制药和电子行业的复杂玻璃几何形状。然而,这需要很长的交货期,限制定制,并导致材料浪费。一种成功的增材制造(AM)方法的开发可以解决这些限制,允许更复杂的玻璃对象生产,以一种可再生和具有成本效益的方式,特别是原型或有限的产量。
迄今为止,已经研究了多种AM方法用于玻璃,包括立体光刻,直接墨水书写,熔融沉积建模,激光粉床融合。然而,它们在分辨率、几何精度和光学质量方面都有各自的优势和局限性。间接方法(立体平版印刷和直接墨水刻写)提供了透明度,但是,由于体积的、通常各向异性的、制造后热处理(去除有机成分)和烧结(烧结)导致的收缩,几何精度受到影响。熔积成型是一种直接的方法,但其分辨率受到喷嘴几何形状和尺寸的限制。激光粉床融合(LPBF)解决了上述局限性,但会导致零件不透明、不透明。
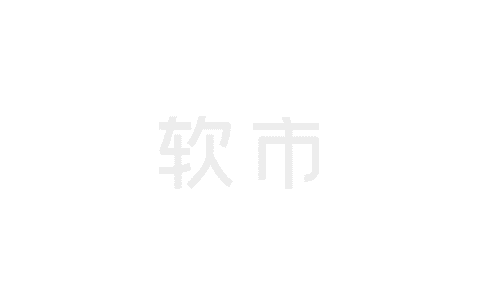
3D打印熔融二氧化硅玻璃。
平均直径为40 nm的非晶态二氧化硅纳米颗粒分散在单体基体中。单体基质主要由单体羟乙基甲基丙烯酸酯(HEMA)组成,由于溶剂化层的形成,可以使大量的二氧化硅纳米颗粒分散,而无需使用进一步的添加剂15。然后用自由基聚合的立体光刻技术对纳米复合材料进行成形,得到了所谓的“绿色部分”。由此产生的绿色部分可以进一步热聚合或通过额外的泛光灯曝光步骤。在开发过程中,通过浸泡在溶剂中去除非聚合材料。绿色部分随后被热降解,即通过加热去除聚合物基质(粘合剂),从而导致热分解,从而形成所谓的“棕色部分”(见上面扩展数据a)。在1300°C的最后烧结阶段,棕色部分的密度(ρfinal = 2.2 g cm?3)增加到没有剩余孔隙和裂缝的高质量熔融石英玻璃的密度。整个过程如上图a所示。热处理程序可以在扩展数据图b中看到。
本论文借鉴了此前相关知识和结论,提供了更详细的描述,并展示了已开发的玻璃激光粉末床熔合工艺的能力。此外,还评估了制造零件的物理和机械性能,并提出了该技术的潜在用途。特别是就2种材料和3种制造方法分别描述了原料材料和制造方法。第4节提供了已开发技术在化工制造业中的可行性示例和潜在用途。第5节概述了用于评估生产零件的物理(几何精度、孔隙率、结晶度)和机械性能的方法。最后,第6节介绍并讨论了生产零件的性能结果,而第7节总结了重要结果和结论。
2.材料
本研究以两种钠钙硅玻璃粉末SLSG109和SLSG44为原料。两种原料的成分基本相同(见表1,由EDX-JEOL 6060LV SEM测定,美国),仅在粒径方面存在差异,以评估其对LPBF玻璃加工的影响。
表1 电子显微镜下玻璃原料的化学成分(按重量计)(a)元素和(b)氧化物。
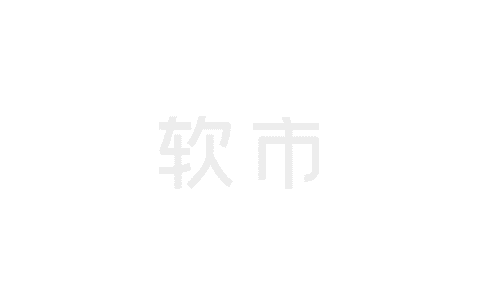
激光衍射(Malvern,Mastersizer 3000, UK)显示,两种粉末的粒径均为高斯分布(图1),SLSG109和SLSG44的平均粒径分别为109?μm和44?μm。SLSG44的高斯分布较宽,表明颗粒数量越大,颗粒间空隙越小,堆积密度越好。相对较细的粉末具有较高的包装密度,一般首选LPBF,因为它们提供了更大的激光加工表面积(22.8?m2/kg的SLSG109相对于58.3?m2/kg的SLSG44)和最小的孔隙率在建造部件。然而,太细的粉末会导致流动、沉积和粉末在构建区域上的扩散困难。
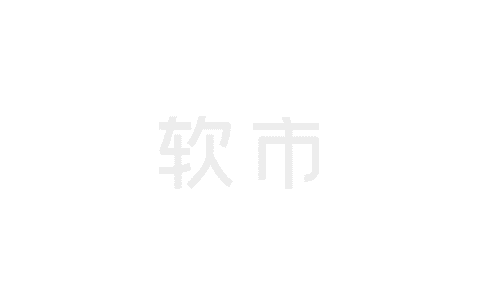
图1 两种玻璃原料的粒径分布和200倍放大率下的SEM显微图。
原料材料包括两种粉末的球形颗粒(见图1)。球形颗粒改善了流动性,从而使粉末沉积在LPBF中[9]。使用FT4粉末流变仪评估两种原料的流动性。基本流动能BFE,即叶片以100%的速率通过样品所需的能量(扭矩和轴向力)发现SLSG44(BFE=168)的毫米/秒更高?mJ)与SLSG109(BFE)相比?=?146?mJ)表明前者的流动性较差(图2)。此外,流量指数FRI,即10时的流量能量比毫米/秒超过100?测量mm/s,以确定进料中的任何粘结性。粘性粉末(FRI>1)对叶片在样品中移动时的流速变化非常敏感。SLSG44和SLSG109的FRI分别为1.22和1.08,表明SLSG44具有轻微的内聚行为。与SLSG109相比,SLSG44的流动性较差,这可能是由于其粒径较小,粒间作用力可能增加并抑制流动性。
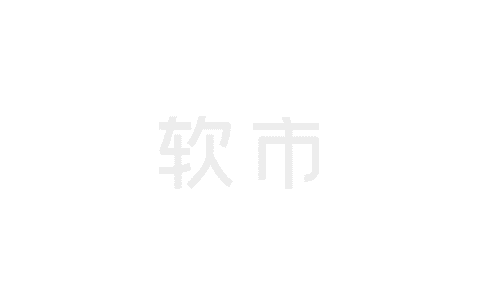
图2 所选玻璃原料的基本流动性能。
差示扫描量热法(Q600-TA Instruments, USA)表明,两种样品的转变和熔化温度非常相似,分别为575℃和1280℃。
3.制造方法
本节介绍LPBF工艺和工艺参数的优化步骤。在第3.1节中,第一步使用单轨,以评估粉末固结,并告知基底的选择。这些发现为研究薄壁结构(通过多层重复线性激光扫描制造)中相邻层之间的相互作用奠定了基础,同时在第3.2节中确定了其加工窗口。这些反过来又提供了关于壁分辨率的见解,该分辨率最终用于通知第3.2节中形成阴影、多层、立方体结构的相邻熔体轨迹之间的阴影间距。
3.1. 激光粉末床聚变
本研究中的LPBF方法采用商业系统(德国ReaLizer GmbH SLM-50)处理所选玻璃原料。SLM-50使用波长为1064的钇光纤激光器纳米。原料材料通过一个自动雨刷系统在一个70英寸的平台上沉积成厚度均匀的层毫米直径的平台。选择层厚度以适应进料中的最大粒径,即70?用于SLSG44和120的μm?SLSG109为μm。平台温度保持在250℃在制造过程中,通过一个集成加热器降低温度梯度,该温度梯度通过制造零件的厚度形成。如果氧气含量增加到0.9%以上,1000升/分钟的氩气流量可确保惰性条件并防止氧化。焦点位置为9.6?本研究选用mm。这是激光二极管和透镜之间的距离,并确定直径光斑大小,在这种情况下对应于20?μm。
基板和原料材料的类似成分通常在LPBF中选择,以实现粘合并适应热膨胀。然而,这项研究揭示了当1?在标准SLM-50钛平台上使用mm厚的钠钙硅玻璃基板,用于玻璃的LPBF,因为在玻璃基板的下表面上观察到蚀刻(图3a)。
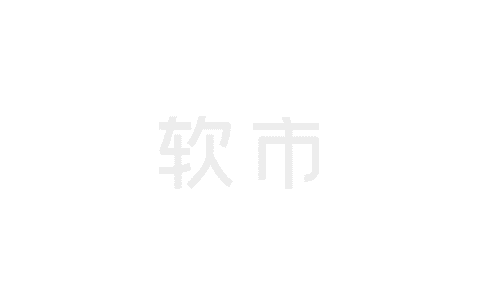
图3 单扫描轨迹上下表面的显微照片(SLSG109,100?W和37?mm/s)形成在固定在(a)钛平台和(b)氧化铝板上的钠钙硅玻璃基板上。
玻璃原料和玻璃基板吸收率低,导致激光照射部分到达玻璃基板下方的钛基板表面。这部分辐射随后被反射并重新定向到玻璃基板,腐蚀其下表面(图3a)。可以通过将玻璃基板固定在反射性较差的基板(如氧化铝)上来防止蚀刻(图3b)。单层设计可以成功创建与此设置(图4)打开了玻璃装饰应用的潜力。然而,玻璃基板上形成的微裂纹会在激光加工多层零件的后续层时传播并最终引发断裂,导致构建失败。氧化铝基板具有比玻璃更高的耐热性和类似的热膨胀系数,因此可以减少热裂,同时提供足够的粘附玻璃。因此,本研究选择厚度为2.5 mm的高纯氧化铝圆盘作为后续研究的对象。
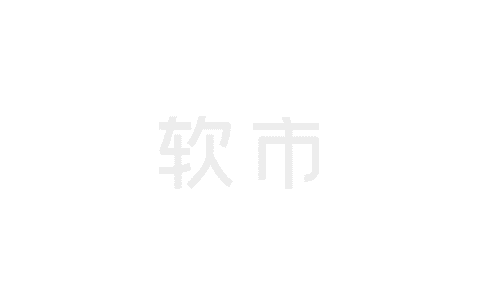
图4 固定在氧化铝板上的玻璃基板上的钠钙硅玻璃单层激光粉末床熔合示例。
3.2. 能量密度优化
制定工艺图以确定两种原料的最佳加工窗口,计算沉积能量密度作为加工参数的函数。考虑到激光功率P、扫描速度v和层厚度t(等式1a),2D方法用于薄壁结构,其中每层单次线性激光扫描足够(图5a-b),而3D方法用于涉及每层多次和相邻激光扫描的零件(图6a-b),还应考虑舱口间距h(方程式1b)。
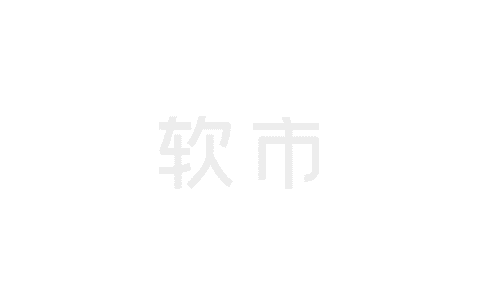
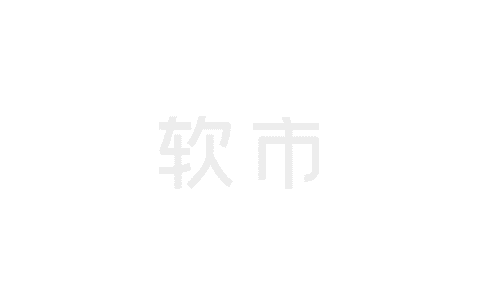
图5 实现薄壁结构固结的过程图,用于:(a)SLSG109和;(b) SLSG44(加固零件为绿色区域,加固不良/未加固零件为灰色区域)。
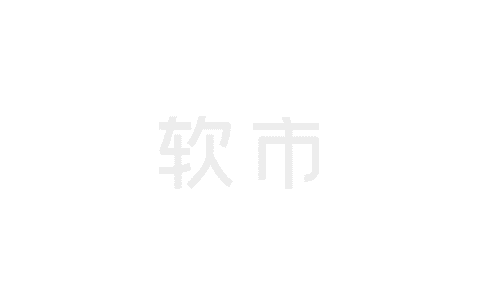
图6 在厚壁结构中实现固结的过程图,用于:(a)SLSG109和;(b) SLSG44(固结零件为绿色区域,不良/未固结零件为灰色区域,或轨道高度过大/精度差的零件为灰色区域)。
研究发现,薄壁结构(图7a) SLSG44和SLSG109分别需要至少27 J/mm2和30 J/mm2才能实现粉末的熔化和固结(图5a-b)。能量密度低于这一极限会导致较差的固结(如图7a所示的例子)。SLSG44和SLSG109的厚壁结构所需能量密度分别在70≤ED3D≤120 J/mm3和65≤ED3D≤110 J/mm3之间(图6a-b)。能量密度低于这一范围会导致固结不良和脆性零件,与低能时的薄壁结构相似,而能量密度超过这一范围会导致成球,因此轨迹高度过高,两种原料的尺寸精度都不高(典型例子如图7b所示)。无论设计的复杂程度如何,这些流程图现在都可用于制造零件;第4节给出了示例。
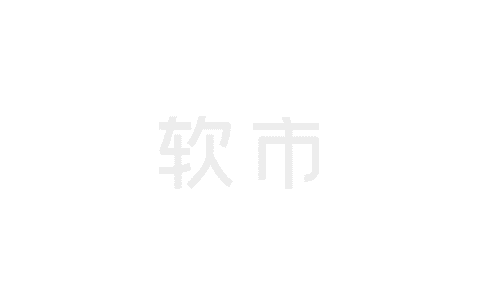
图7 玻璃LPBF: (a)固结良好(左)和固结不良(右)的薄壁结构;(b)立方体结构,固结不良(左)、固结良好(中)、成球(右)。
两种原料的薄壁和厚壁零件的加工窗口非常相似。因此,对于相同组成的原料,能量密度的影响与粒度无关。然而,当使用更细的粉末时,层厚度可以减小,例如,最小允许层厚度为70?SLSG44与120的μm?对于SLSG109为μm,这反过来又导致更高的分辨率。薄壁光学显微镜(每层重复单次激光扫描,图7a)证实了这一点,表明在相同能量密度下,SLSG44比SLSG109获得了更高的分辨率,即更小的壁厚(图8)。与SLSG109相比,在相同的能量密度下,SLSG44获得的最小特征值为575μm,而SLSG44的最小特征值为385μm。由于这些原因,使用SLSG44制造的零件在本研究中仅随后进行了评估。
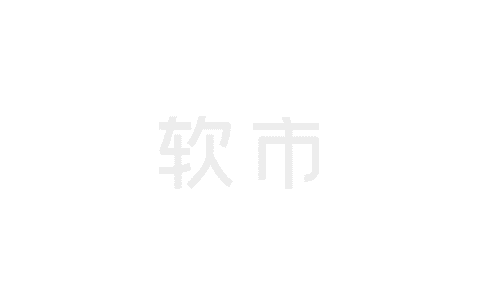
图8 对于薄壁零件的分辨率作为两种原料所选能量密度的函数。
4.可行性示例和潜在应用
如图7所示,使用激光粉末床熔接制造的玻璃零件不透明。这归因于存在表面的、部分熔融的粉末颗粒和内部缺陷(详细讨论见第5.2节)。尽管透明度是可取的,但在某些应用中,几何复杂性与化学惰性的结合更为重要。此类应用可在制药和化学制造行业中找到,包括:
4.1. 连续流反应器(CFR)
这些通常涉及多个入口,这些入口以精确的流速将反应物供应到一系列通道中,这些通道的几何形状针对特定化学反应的混合和停留时间进行了优化。
玻璃的LPBF可用于制造CFR,结合玻璃的惰性,提供定制的机会。这些可以以现成反应器的形式制造,也可以作为单独的通道制造,这些通道可以与传统配件结合集成在模块化CFR系统中。图9a-c中提供了各种几何形状的流动反应器通道示例,作为概念证明。零件表面的部分熔融粉末颗粒(使用LPBF制造)可能为更好地混合反应物提供额外的优势,类似于在传统CFR中使用挡板。
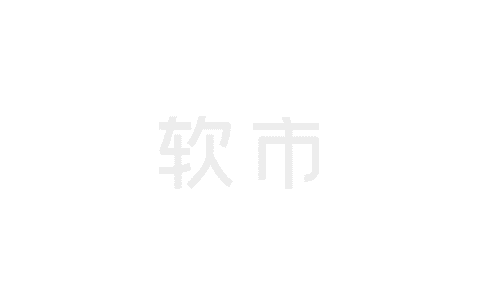
图9 连续流反应器通道:(a)线性圆柱形通道(10?毫米长和2?毫米内径,(b)角通道(12.5?mm长/侧边和3?直径(mm)和(c)U形槽(10?毫米长和2?毫米内径)。
4.2. 整体结构催化剂
它们以网格、微通道反应器甚至晶格的形式存在。玻璃的LPBF提供了一个机会,可以创建高分辨率的复杂几何形状,可以用作结构化催化剂,而无需任何模具的先决条件。定制是AM的一个主要优势,因为结构化催化剂几何形状可定制以增加表面积,随后可使用催化活性材料进行功能化,以适应不同化学制造工艺的不同要求。图10a-c展示了通过LPBF产生的可能用作结构化催化剂的玻璃几何形状的示例。表面的、部分熔融的粉末颗粒的存在可额外增加可用表面积并提高催化剂的效率。
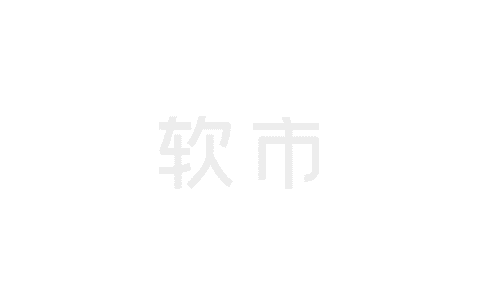
图10 结构化催化剂示例:(a)网格状矩形(7?×?7 × 1?mm3),(b)陀螺网络晶格(20?×?20?×?20?m3)和(c)菱形网络和BCC晶格(10?×?10?×?10?mm3)。
对于上述应用,玻璃的LPBF可以是传统制造技术的一种经济高效的替代品,即高度定制,用于有限生产量的原型制作或制造。LPBF可以克服与传统制造方法相关的额外成本,例如:(a)玻璃浇铸工艺中的模具制造或:(b)减法制造工艺(通常用于CFR的微机械加工、激光烧蚀或蚀刻)的长前置时间,同时实现更快的周转。然而,与其他AM工艺类似,与传统铸造工艺相比,随着产量的增加,LPBF的成本优势逐渐减弱,因为模具制造的额外成本可以在众多制造零件中吸收。
5、物理机械性能评价方法
本节介绍了使用玻璃LPBF制造的零件中确定设计极限、孔隙率、结晶度和弯曲强度的评估方法。
5.1. 几何极限
采用SLSG-44对线性空心圆柱形通道进行LPBF(类似于连续流反应器中使用的通道),以进行几何优化(图9a)。这涉及到设计极限的调查,考虑到壁厚,内径和通道长度的直线通道与圆形截面。共考虑了72个设计参数组合;设计壁厚(tw)之间的远程0.2≤tw≤0.4毫米,0.1毫米的增量,而设计的内部直径(Din)和长度(L)介于0.5≤Din≤2.0毫米之间,增加0.3毫米和5 L≤≤14毫米,递增分别为3毫米。光学显微镜也被用来确定设计和实际的几何形状之间的差异。
5.2 缺陷和孔隙度
用微型计算机断层扫描(CT, ZEISS, XRADIA Versa XRM – 500, Germany)对LPBF和SLSG44制造的成品件的孔隙和缺陷进行了研究。特别是两个5×5×5 mm3立方样品,使用图6b中最佳处理窗口的边界制造(即79和108 J/mm3),进行了评估。x射线辐射根据x射线衰减系数的分布提供内部特征的截面信息。输出是8位灰度图像,其像素的特征是灰度强度因子(0到255之间)。CT切片的分辨率为4μm。随后,通过开源软件ImageJ中的Java脚本处理图像,以确定其孔隙度(步骤如图11所示)。第一步涉及到二值化,即像素转换为黑色“0”和白色“1”,使用的是一种区分毛孔和玻璃结构的图像分割算法。图像分割后,ImageJ自动计算出多孔面积和总截面积。前者与后者的比值提供了每片样品的孔隙度。
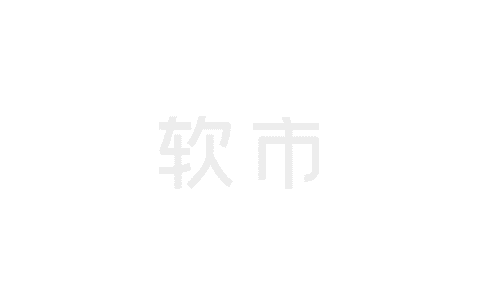
图11 孔隙度分析程序:(a)玻璃立方体的显微CT切片,(b)背景去除,(c)图像分割和(d)孔隙提取。
在图像分割中,通常需要一个阈值来对黑白灰度像素进行分类。文献中有多种阈值方法,它们对应用程序类型和数据高度敏感。在本研究中,我们选择了Otsu的阈值算法,因为我们发现它对于玻璃珠CT切片和[12]中的无损检测图像都是可靠的。聚类方法通过用两个高斯分布近似直方图来分离前景和背景类中的像素。Otsu的方法通过最小化前景和背景类的类内方差或等价地最大化它们的类间方差来定义阈值。尽管存在局部自适应阈值方法,并且可以根据邻近像素对每个像素进行单独的分割,从而提高其可靠性,但它们的计算量非常大。此外,它们通常依赖于初始阈值或需要控制器的手动监督。由于这些原因,本研究没有考虑到他们。
5.3. 结晶度
使用X射线衍射(Bruker,D8 ADVANCE,USA)对上述两个立方体样品的分子结构进行额外评估,以确定激光处理后玻璃珠的非晶态结构是否保持不变。
5.4. 抗弯强度
玻璃是一种脆性材料,缺乏屈服和重新分配应力的能力。因此,任何缺陷都是一个潜在的应力集中点,当受到一定程度的张力时,它可能会传播并导致断裂。因此,评估玻璃的弯曲或拉伸强度变得至关重要。通常,玻璃最好进行弯曲试验,因为弯曲试验可防止夹持位置的错位和破坏问题,而夹持位置通常与脆性材料的拉伸试验有关。
因此,使用三点弯曲(3PB)试验确定定制微型蠕变试验台中棱柱试样的弯曲强度(图12a-b)。使用垂直于其最长轴(z)的LPBF和SLSG44制造了四个系列的24个样品,尺寸为1×2×8 mm3。三个系列涉及沿横截面短轴(x)的线性扫描,能量密度分别为79、93和108?J/mm3,而第四个涉及沿横截面长轴(y)的线性扫描,能量密度为108?J/mm3(表4)。所有样品在560℃下退火两小时℃(加热和冷却速度为2?),在机械试验之前,以消除任何残余应力。3PB装置的支撑跨度为5.35?当应变速率为0.0005时?s-1。随后使用公式2计算破坏应力:
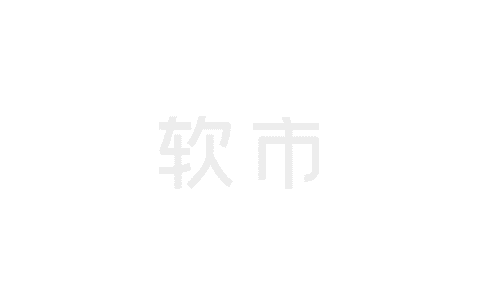
其中Pf为破坏荷载,ls= 5.35 mm, b= 2 mm, d= 1 mm分别为棱镜的支撑跨度、宽度和高度。
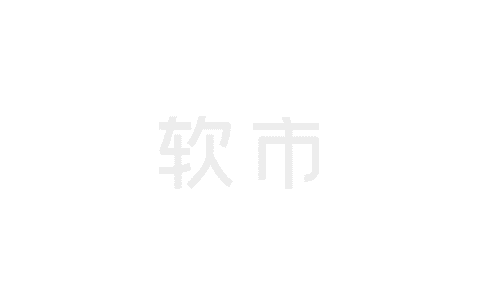
图12 三点弯曲:(a)样品和(b)设置。
表2 LPBF生产的流动反应器通道的设计极限。
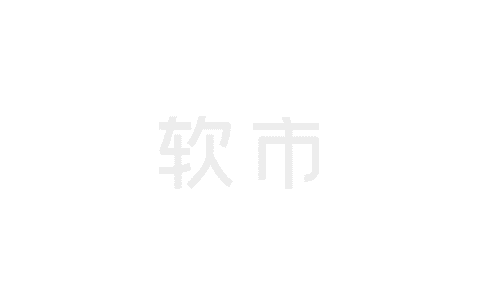
表3 壁厚结果的尺寸精度。
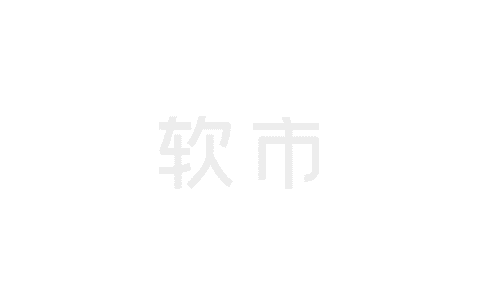
表4 用SLSG44的LPBF在处理窗口的最大和最小能量密度下制备的立方体样品的孔隙度。
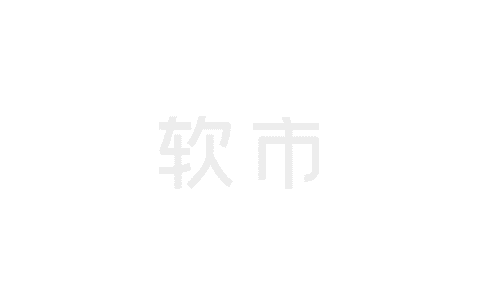
玻璃在非惰性条件下测试时,对亚临界裂纹扩展很敏感。亚临界裂纹扩展通常通过将每个试件的破坏应力转换为时间等效强度来归一化。为此,利用公式3中的Brown将3PB试验的斜坡应力历史转换为参考时间段tref= 60 s的恒定应力。
其中tf为失效时间,σf,60为参考时段的失效应力,n为静态疲劳常数(对于苏打、石灰、硅玻璃和普通实验室条件,n = 16)。
根据玻璃强度数据加权最小二乘回归的建议和程序,对结果进行统计分析,并拟合成 2-parameter威布尔分布(公式4)。
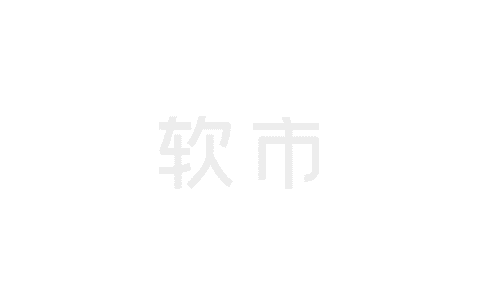
其中Pf为破坏概率,β和θ分别为Weibull 分布的形状因子和比例因子。
6. 结果与讨论
6.1. 几何限制
最低允许设计直径和长度进行了不同壁厚(表2)。设计长度14毫米可以实现没有开裂时设计壁厚0.2毫米的最大允许同时使用设计时设计长度减少到8毫米壁厚增加到0.4毫米。较厚通道的长度限制是由于每层沉积的能量输入较大。更大的能量输入产生了积累热量的区域(在制造过程中观察到的亮橙色区域),增加了建筑部件的温度梯度,并导致热应力的发展,最终开裂。
用光学显微镜进一步研究了尺寸精度。结果表明,从设计到制造,所有通道的外径、Dout和壁厚均增大,内径减小。当tw = 200μm时,实际厚度为620μm;300μm和400μm的实际粒径分别为979μm和1168μm(表3)。样品外径平均增加17.5% ~ 19.7%,内径平均减少34% ~ 46%。
尽管设计尺寸和制造尺寸之间存在显著的偏差,上述差异对所有样品来说都是相当一致的。因此,在CFR的设计阶段,它们可能被考虑在内,以预测其实际尺寸,反之亦然,以计算所需的设计尺寸,以达到预期的制造尺寸。
6.2 缺陷和孔隙度
Micro-CT显示三种类型的缺陷随机分布在整个样品(图13a): (a)孔隙,(b)含有未烧结粉末颗粒的区域和(c)裂纹。孔隙是完全封闭的,没有相互连接,这有利于固体壁连续流反应器的应用,以确保泄漏密封性。在陶瓷的LPBF中,裂纹主要出现在靠近基体的下表面,这与制造过程中产生的温度梯度和热应力有关。将基板温度提高到250℃以上,略低于所选玻璃原料的转变温度,有望减少热裂。最后,含有未烧结粉末颗粒的区域主要集中在立方体的顶表面附近。远离顶部表面的层暴露在大量的激光扫描下,因为部分未吸收的激光照射穿过玻璃样品,并重新处理之前的层,巩固任何粉末颗粒,从之前的扫描完好无损。这表明最后的表面扫描可以用来减少这种缺陷。
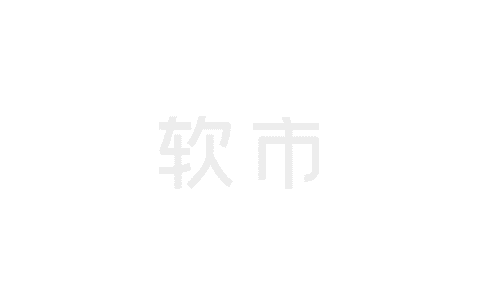
图13 玻璃LPBF构件的孔隙率和缺陷:(a)含有典型缺陷(孔隙、裂纹和未熔
来源:长三角G60激光联盟
声明:本站部分文章及图片转载于互联网,内容版权归原作者所有,如本站任何资料有侵权请您尽早请联系jinwei@zod.com.cn进行处理,非常感谢!