本文选自《智慧企业之路》第二期,第8页,“本期关注”栏目
作者/吴贻君
一、数字样机的概念分析
传统产品设计一般采用“物理设计”方式,通过经验设计+物理样机试制试验来完成。自上世纪80年代以来,随着计算机硬件的成本下降,CAD技术得以迅猛发展,并在汽车行业(如:GM)和航空行业(如:Boeing)得到广泛应用。经过数十年的发展,CAD、CAE、CAM等技术和工具日益成熟,数字化建模、虚拟仿真、数字化工艺设计等逐渐融入到产品的研发过程,制造业已改变了传统的研发模式。
随着单点工具在研发过程中的深度应用,工业企业和软件行业均希望通过一套相对统一描述、组织、管理和协同运行的方法,来支撑产品研发全生命周期上的一致表示与信息交换共享,因此数字样机/数字化样机/虚拟样机“Virtual Prototype(VP)”等概念逐渐被提出和应用。
二、数字样机技术发展简史
数字样机的“前世”
在数字样机的发展过程中,不同的提出方往往根据自身立场,进行了不同方向的解读,笔者进行了概括性的梳理,大致包含以下类型:
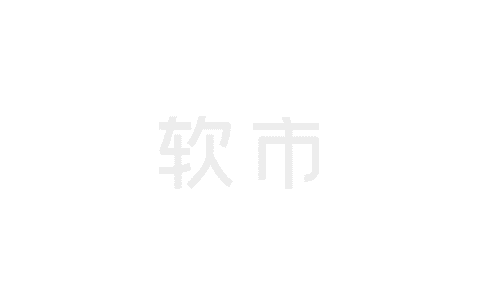
▲图1:数字样机的类型
● 几何样机:往往特指机械/机电产品的整体和模块的数字化“静态”模型,用于表达产品尺寸信息、材料信息等。
● 概念样机:针对产品研发早期的系统级描述和仿真模型,考虑产品在具体工作环境中的工作模式、运动过程。
● 性能样机:一般指产品整机到模块层级的多学科/多物理场性能仿真“动态”模型,如:结构强度、动力学、散热、电磁兼容等。
● DMU(Digital Mock—Up)数字化样机/数字原型:作为几何样机的延伸,增加装配制造、工艺等信息。
● 功能样机:借用DMU的概念,但是应用在产品的早期设计过程,一般指产品概念设计阶段的产品功能模型,包括产品的逻辑架构、功能流、接口关系(如:ICD)、工作时序的设计及验证。
● 虚拟样机:概念等同于几何样机+性能样机,试图通过一套体系描述整个产品从设计到仿真全过程的信息。
● V&V/IVVQ:针对建模与仿真校核、验证与确认(Verification、Validation and Accreditation),该项技术关系到数字样机模型的可信性,现在很多数字样机的论述中亦将其纳入。
● Digital Twin(数字孪生):作为工业界提出的全新概念,期望通过高精度的产品模型,应用于产品设计、制造、运行的全生命周期,并通过传感器技术实现与产品真实状态的完全“虚拟化”同步。
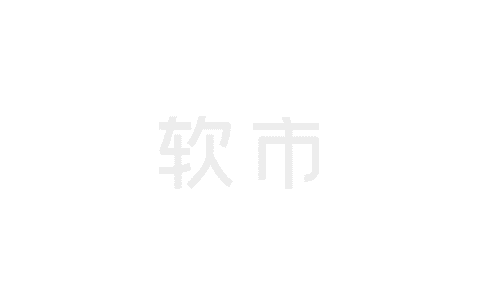
▲图2:系统不同过程对应的样机形态
通过对上述概念的解析,不难发现各类样机的共性及差异性:
◆ 共性:数字化、模型化表达,甚至是不同工具开发的、已有的子模型组成的模型组合/网络;
◆ 差异性:应用领域的不同,分别满足阶段、过程的数字化协同设计、验证及评估。
数字样机的“今生挑战”
针对上述样机的内涵和应用场景,各软件服务商以及航空、航天等领域的研发机构均开始进行数字样机技术的梳理与总结。以国内的军工行业为例,笔者走访了多家单位,均在近期或者“十三五”信息化建设规划中提出构建面向自身产品的数字样机体系,并且均对数字样机的建设内容存在疑点,主要集中在:
● 数字样机的承载与呈现:
认为和传统的数字几何样机相同,可以采用类似于CAD模型的直观表达,呈现产品的全要素、全性能;
● 数字样机的产生环境:
认为客户通过一套工具完成构建-虚拟化验证的完整过程;
● 数字样机的关联形式:
认为完整的数字样机体系应该是“机-电-液-控/软”等学科紧密集成的,可以实时呈现相互影响的动态关联。
在当前的基础研究和软件条件下,上述设想在未来一段时间内是完全无法实现的。在此有必要站在产品研发的全生命周期的维度,剖析当前各阶段样机的形态、应用价值、支撑环境。
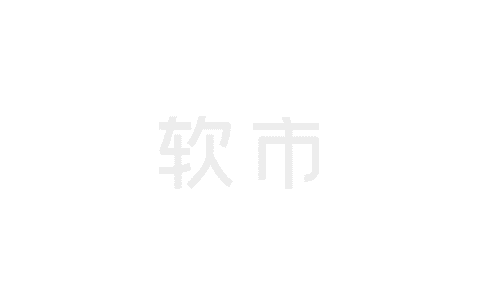
通过对上述分析,不难发现传统信息化建设与数字样机体系建设的冲突如下:
● 重工具、轻体系,很难针对研制全过程、全要素的表达和应用。
● 各自为政、耦合困难,已有工具来自不同厂商,导致模型/数据的交联、传递存在很大困难。
三、未来数字样机的发展趋势
先进企业经验分享
为支撑智能研发的落地,需要从概念解读、技术储备、工程应用等维度重新考虑数字样机的发展方向。笔者通过对国内外的先进企业以及软件厂商提出的概念和建设思路进行了梳理,一些可借鉴的观点如下:
◆ 洛克希德.马丁
在《Next-Generation Virtual Prototyping》一文中,提出“数字样机(虚拟样机)应支持产品全生命周期并可适用于整个系统工程从概念设计到训练的多种需求,它应该捕获所有与产品定义相关的信息,提供与产品行为全方位交互的机制”,并提出了SAM(系统架构模型),用于构建产品需求、行为、结构、特性及各要素相互关系信息,用于支撑各个部门协同工作,洛马称该过程为“连线成缎Turning Threads into A Tapestry”。
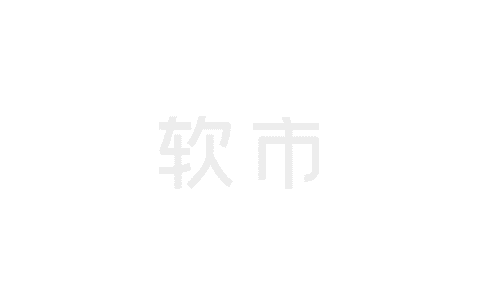
▲洛马连线成缎过程
◆ 泰雷兹
自2013年以来,通过MBSE(基于模型的系统工程)的推广应用,实现提升数字样机的应用深度与广度,达到对雷达功能和性能领域的多层次、多维度的数字样机构建。期望通过同一套标准的数字样机模型,实现不同人员的应用(原文直译为:满足不同利益相关者的“投射”)。
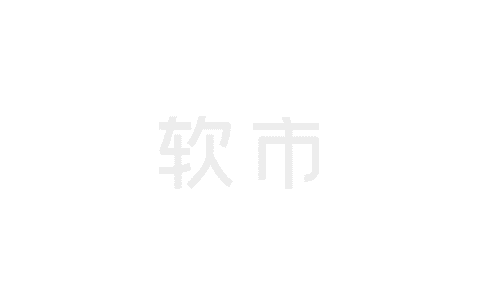
▲泰雷兹多领域/多层级雷达模型体系
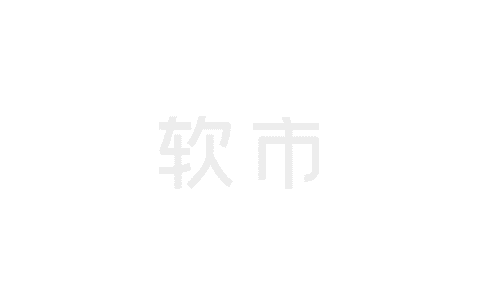
▲数字样机面向不同利益相关者的“投射”
◆ 中航工业某企业
针对面向产品制造的研发,在规划和调研新的支撑平台,采用一套新的描述模式以及管理流程,实现研发、制造全过程的数字量连续传递。
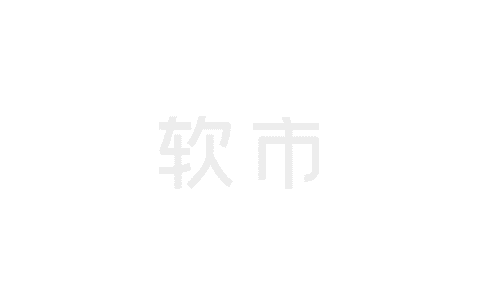
▲数字量从设计到制造的连续传递过程
未来数字样机建设核心内容
通过对先进企业的剖析,在当前研发能力支撑和现状的基础上,初步梳理了未来数字样机建设的核心内容,具体如下:
◆ MBSE技术的推广应用。通过一套可落地的、适用于企业特点的方法论和工具,实现各类样机和模型的关联,构建出“需求-设计-分析验证-管理一体化”的模型网络。
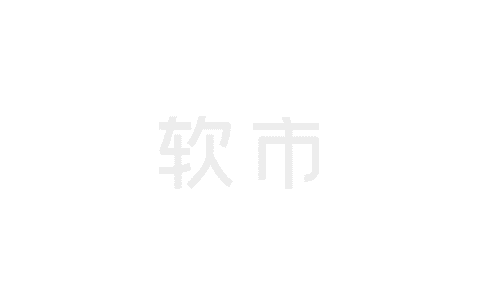
▲基于统一的、全面的、关联的模型网络
◆ 基于统一标准的模型“紧耦合”技术,实现异构模型的联合设计仿真。当前基于FMI标准接口的模式越来越得到主流软件厂商和研发企业的接受和支持。该技术既满足了模型的集成应用,同时又保证数据/知识的安全性;
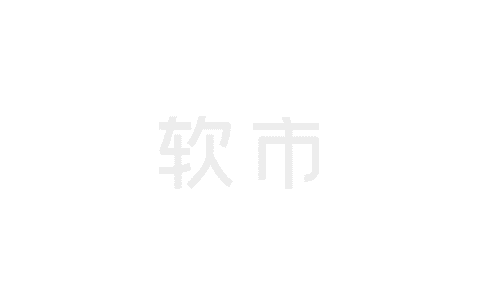
▲基于FMI标准接口的模式
基于通用集成框架的协同仿真技术。针对多学科集成化设计仿真过程,可以采用协同仿真平台实现异构/不同厂商的工具串联,实现后台“参数级”数据的传递,以及多方案的迭代优化。当前市场主流的平台环境包括:达索的Isight/SLM、MSC的SimManager、Altair的HyperWorks/ADM、Phoenix Intergration的ModelCenter。
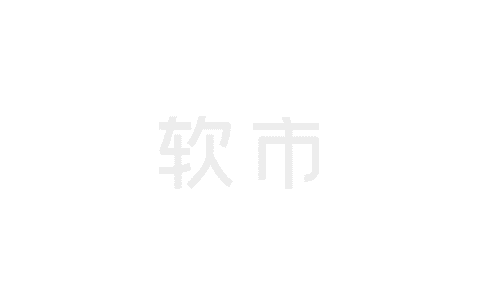
▲基于某集成框架实现需求-CAD-CAE的集成应用
四、研发企业数字样机建设的几点建议
笔者结合多年来的信息化规划和建设经验,认为研发企业数字样机体系建设是一个长效的、革命性的工作,很难直接照搬照抄其他企业的经验。因此,对研发企业数字样机建设提出以下几点建议:
◆ 数字样机的建设不等同于软件的购买
由于是覆盖产品研发全阶段、全要素的能力提升,很难通过工具构建和单点能力堆砌来完成。需要综合考虑以下因素:
1)产品研发流程的梳理与变革;
2)适用自身的建模方法论;
3)适用企业运营的协同环境。
◆ 数字样机呈现形式的“合理化”
数字样机不是某一特定形态的结果交付,而是融入到研发过程的结果集合。以航空整机为例,应包含需求指标体系、机电软架构模型、DMU、多物理场仿真模型等等。
◆ 数字样机建设不要追求大而全、要量体裁衣
需要结合企业自身状态,一般遵循“设计仿真工具补齐→典型阶段的协同设计仿真环境建设→全阶段MBSE的建设与应用”三步走策略。
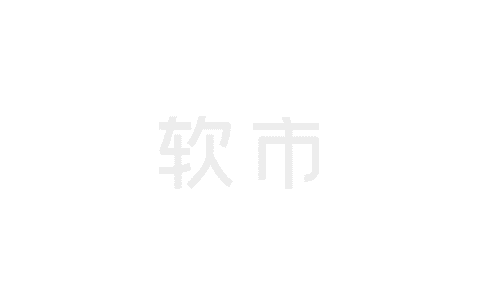
▲某电子研制企业的建设历程
注:本文所包含的文字、图片等内容,均为原创或授权转载。未经《智慧企业之路》书面允许,任何单位和个人不得转载、摘编或利用其它方式使用,已获得授权使用作品的,应在授权范围内使用,并注明”来源:《智慧企业之路》XX年第X期”。违反上述声明者,本公司将追究其相关法律责任。读者联系邮箱:marketing@glaway.com
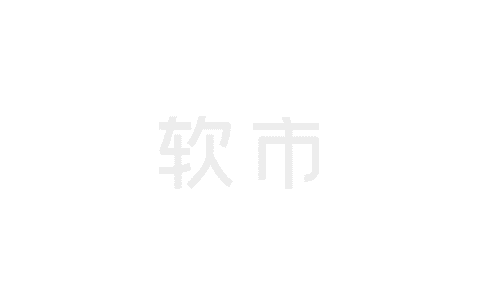
来源:国睿信维
声明:本站部分文章及图片转载于互联网,内容版权归原作者所有,如本站任何资料有侵权请您尽早请联系jinwei@zod.com.cn进行处理,非常感谢!