秦 利1 李 帅1 何 轩1 王 丽2
1 北京航天发射技术研究所 北京 100076 2 中集海洋工程研究院 烟台 264670
摘 要:对某型号火箭海上发射架进行了结构优化设计、静力学有限元仿真及试验分析。依据总体需求与工作流程,通过建立三维及简化后的壳体计算模型,对在不同边界条件下发射架刚强度进行对比,得出优化的结构布局,并结合实物加载试验与仿真结果进行数据分析,进一步验证了结构的合理性与可行性,为在恶劣海况下筒箭组合体的起竖与下放提供了保障。
关键词:发射架;刚强度;海上发射;结构设计
中图分类号:TH123 文献标识码:A 文章编号:1001-0785(2020)03-0070-04
海上发射架在与筒箭组合体起竖过程中受复杂海况影响会产生附加惯性力,伴随起竖过程中筒箭质心位置的升高,回转点处所产生的弯矩也相应增加,因此为保证筒箭安全和发射的可靠性,发射架自身在具有足够强度的同时,还需具有较高刚度。本文在对发射架进行三维设计、模型简化及仿真分析的基础上,结合加载试验,验证发射架设计的合理性与可行性。
1 工作原理与理论分析
1.1 工作原理
发射架(如图1 所示)通过固定架端的两个卷扬机,在指定的时间及速度下牵拉钢丝绳实现起竖架及筒箭组合体的起竖动作。其中固定架与发射船固定连接,筒箭组合体与起竖架通过托座与回转轴连接,起竖到位后,固定支架对起竖架提供限位保护。
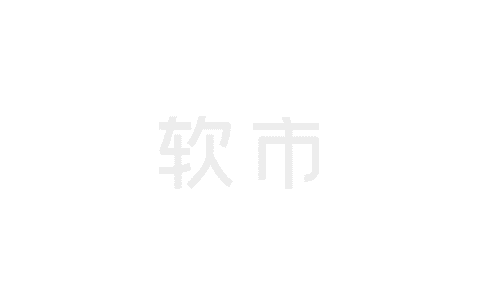
图 1 起竖架工作示意图
1.2 理论分析
起竖架在满载起竖过程中,筒箭组合体所受总弯矩
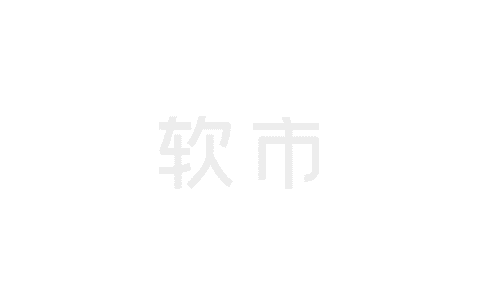
利用式(1)并考虑筒箭组合体全长、结构阻尼及一阶固有频率等初始参数,即可得到其总弯矩值受发射船横摇幅值(纵摇方向筒箭与起竖架为铰接关系,故影响较小)影响最大的结论(航速为0 时,5 级海况下船体横向最大倾角为12.87°)。
因此,理论上将筒箭与发射船间的运动“隔离”开,才能从根本上保证产品的使用安全,而这个重要载体即为发射架自身。
2 发射架设计与仿真
2.1 起竖架
图2b 所示起竖架即为利用拓扑优化[2] 后的结构布局,与方案阶段(见图2a)相比,部分接口位置发生变化,并为优化力的传递路径、改善结构刚度进行一些改动。具体包括:
1)在总质量不变的基础上,将10 mm 厚方钢管改为拼焊形式,其中竖板厚20 mm,横板厚30 mm;
2)起竖架与固定支架的回转铰点设置在结构上方并进行局部加强。
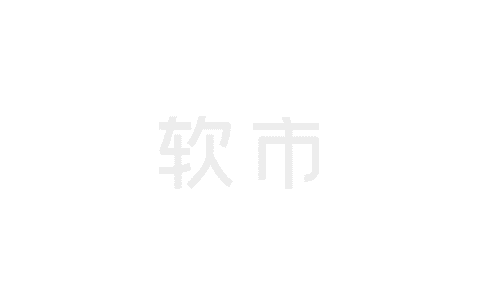
(a) 方案设计阶段
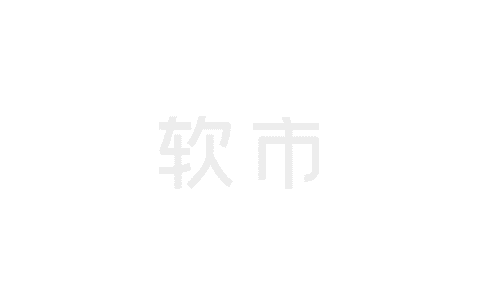
(b) 技术设计阶段
图 2 起竖架优化设计结构示意图
从三维建模软件导入起竖架模型至Ansys 中,所做的前处理工作如下:
1)将实体模型转换为壳体,赋予各截面厚度及方向属性;
2)设置各壳体间的线- 线及线- 面搭接位置为Bonded 接触;
3)设置网格单元尺寸为2 mm,节点数量约32 万。计算工况、约束及边界条件汇总见表1。仿真结果见图3。
其中, 侧向风载荷采用CCS 规范计算, 有
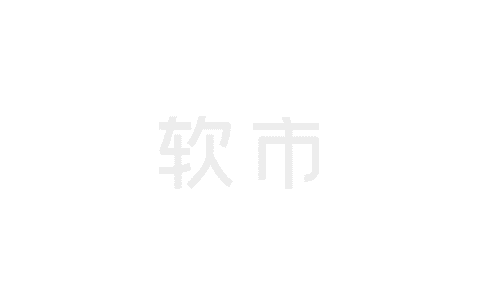
式中: P 为风压;V 为设计风速,为22.5 m/s;S为结构正投影面积(面积投影法未考虑遮蔽影响,但计算结果满足工程需要[3]);Ch 为高度系数;Cs 为形状系数。
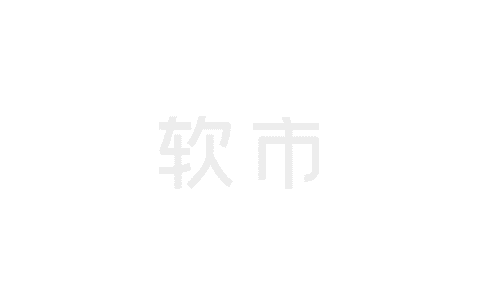
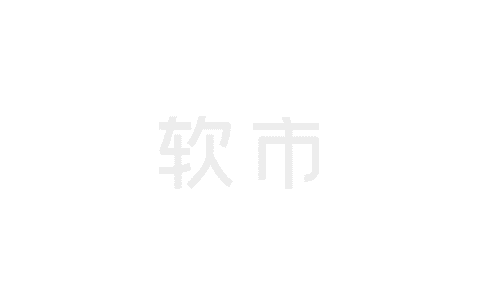
(a) 起竖瞬间工况
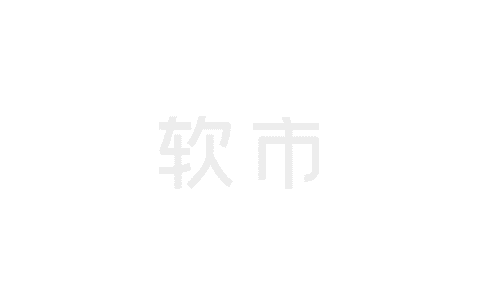
(b) 起竖到位工况
图 3 起竖架仿真结果示意图(横向变形值)
从图 3 可以看出,在恶劣工况下,起竖瞬间的起竖架横向最大变形为16 mm,小于发射筒在满载起竖工况下最大变形量;最大应力在斜筋与纵梁搭接位置处,为272 MPa,满足与筒箭组合体的匹配。
2.2 固定架
固定架下方的6 个支座与发射船甲板固定连接,在设计过程中使用桁架结构优化减重,并在起竖架回转轴及卷扬机附近进行局部加强。
计算模型的前处理同起竖架,计算工况及边界条件见表2, 仿真结果见图4。
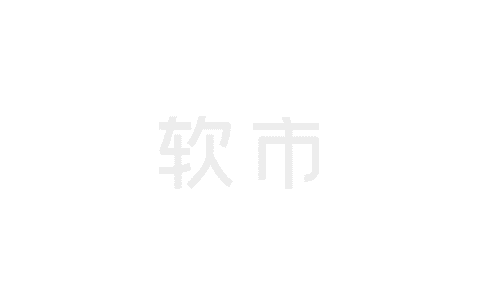
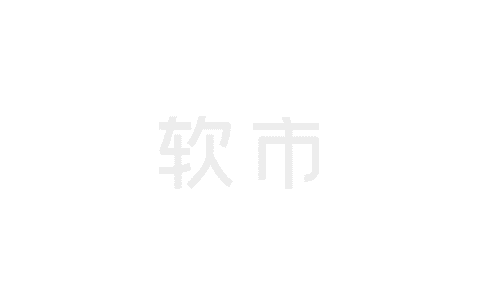
(a) 起竖瞬间工况
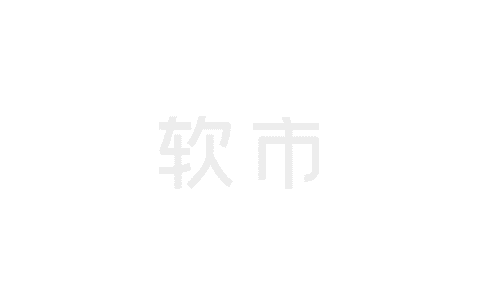
(b) 起竖到位工况
图 4 固定架仿真结果示意图(变形云图)
固定架变形云图见图4,起竖瞬间及起竖到位的最大总变形分别为18 mm 和29 mm,其中横向变形分别为3.8 mm 和15.1 mm,在起竖到位时固定架与起竖架的叠加总变形为23.2 mm,小于发射筒在满载起竖到位工况下最大变形量,满足要求。最大应力出现在固定架上方定滑轮安装位置处,为295 MPa,满足要求。
3 发射架加载试验
3.1 试验要求
基于上述分析,对发射架开展加载试验,与理论计算进行对比验证。试验测点位置见图5。
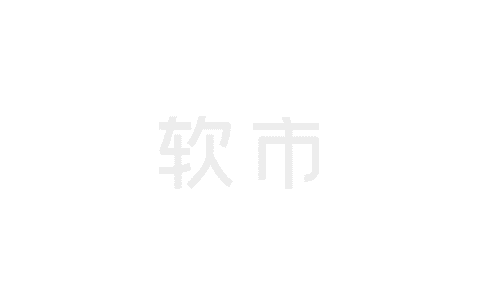
图 5 加载起竖试验测点布局图
试验要求如下:
1)在起竖架上通过增减配重的方式进行加载起竖试验(在加载试验前先进行空载试验以验证试验过程无其他问题);
2)在图5 所示位置布传感器(精度±5%,采样频率100 Hz);
3)分派操作岗位人员:现场总指挥1 人、控制岗1 人、多媒体记录岗1 人及技术安全岗1 人;
4)试验次数为3 次。
3.2 试验结果对比分析
除考虑传感器自身测量误差、真实试验条件与仿真模型存在出入以及天气等客观因素外,可认为试验数据与理论仿真一致,即所设计的发射架结构形式满足要求。
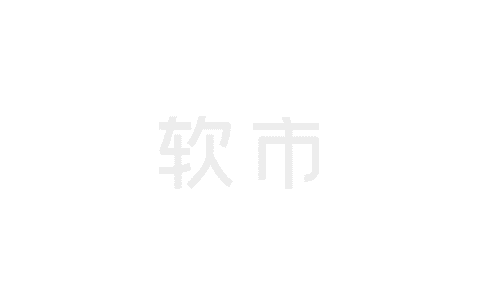
图6 试验现场图
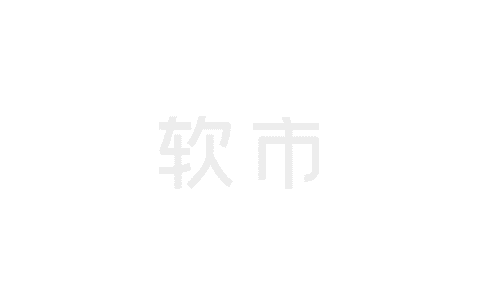
4 结论
通过对海上发射筒箭组合体在起竖过程中所受惯性力进行理论分析,对起竖架进行三维优化设计。通过有限元仿真,定量计算恶劣海况下起竖架的横向最大变形量,经完善后的起竖架结构满足筒箭实际使用工况。实物加载试验进一步验证了结构设计的合理性。
实际上双卷扬起竖方案存在单根失效的理论可能,从产品使用安全性出发,发射架在设计过程中也综合考虑了单卷扬偏载起竖及下放工况,可满足使用要求。在实际应用时,还需充分考虑在不同海域下发射架结构自身适应复杂海洋环境腐蚀的能力,以综合评估其使用寿命。
参考文献
[1] 殷金龙. 海上火箭发射稳定平台的设计与仿真研究[D].哈尔滨:哈尔滨工程大学,2016.
[2] 杜子学,罗辉. 基于拓扑优化的厢体骨架结构优化设计[J]. 机械设计与制造,2016(2):236-240.
[3] 林一,胡安康,蒋玮. 海洋平台风载荷的数值分析[J].船舶工程,2014,36(1).
来源:起重运输机械
声明:本站部分文章及图片转载于互联网,内容版权归原作者所有,如本站任何资料有侵权请您尽早请联系jinwei@zod.com.cn进行处理,非常感谢!