螺纹钢作为现代建筑的基本材料应用广泛,在轧制过程中,如果不能及时发现表面存在的缺陷,会导致生产出大量废品,因此需快速检测出螺纹钢存在的缺陷,以便工作人员及时调整轧机压力或更换轧制设备。
目前螺纹钢缺陷多采用人工检测,在螺纹钢生产过程中, 对每一根坯料轧制出的螺纹钢产品,都要按照国标要求或企业内控标准进行样品离线实验室检测,检测内容包括:样品的尺寸、表面、重量等, 一般每 15 至 20 分钟左右检测一次,一旦检测出超过范围的上述问题需要及时报警,以便工作人员及时检修设备。
由于生产现场环境恶劣、劳动强度大、操作危险、人工检测效率低,距离生产点远时效性差等因素,使各个螺纹钢生产企业, 都迫切需要自动快速智能分析报警系统来破解这一难题。
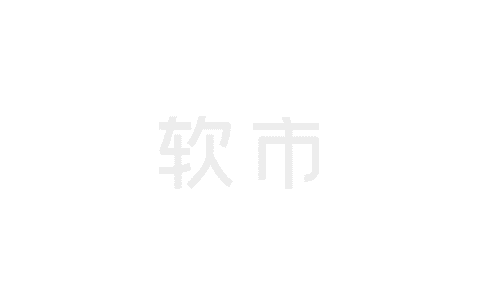
本文研究基于机器视觉的螺纹钢表面缺陷检测方法,以提高螺纹钢生产的可靠性、产品质量和生产效率,推动我国螺纹钢生产行业向“智能制造”转型升级。
01螺纹钢表面缺陷检测技术综述
传统无损检测阶段
早期的螺纹钢表面缺陷无损检测方法主要分为人工检测法、 涡流检测法、 漏磁检测法、 红外检测法等。
现在中国仍有大多数企业采用人工进行产品表面缺陷的检测, 该方式灵活性高、成本低;但其检测结果容易受检测人员检测标准的影响, 随机性大, 存在较多漏检、误检情况, 而且当检测人员工作强度大时, 检测效率低下。
涡流检测法是借助电磁感应原理,根据待测螺纹钢内感生涡流的变化来判定螺纹钢表面是否存在缺陷,适于检测凹坑等较大的缺陷,不适于识别麻点缺陷。
漏磁检测法的基本原理是依据螺纹钢缺陷的铁磁特性, 根据漏磁通密度与表面缺陷的体积成正比的关系, 直接测量漏磁通密度来检测表面缺陷的大小并进行分类和识别。
红外检测法是一种利用红外辐射的原理对螺纹钢内部的能量流动情况进行测量与分析的无损检测方法。通过螺纹钢表面的温度变化来反映其表面的物理特性,当存在缺陷时, 物体表面温度的升高, 从而实现检测功能。
机器视觉阶段
⑴激光扫描阶段
激光扫描技术是利用激光器发出的激光扫描钢材表面,然后利用图像处理技术或者信号处理技术对扫描表面获取的二维信号进行处理,以完成缺陷信号的检测和识别。国内最早使用激光自动检测钢材表面质量技术的地区是宝钢, 该方法检测灵敏
度高、 实时性强, 但容易对小面积缺陷或者低对比度的缺陷产生漏检、 误检的情况。
⑵基于 CCD 成像的机器视觉检测阶段
基于CCD成像的机器视觉的表面缺陷检测技术是在不同光源与CCD相机的配合下获取样本表面的信息, 利用数字图像处理技术对图像表面信息进行分析处理, 然后提取所需的缺陷特征, 最后对所选特征进行识别或分类预测。
与其它检测方法相比, 基于机器视觉的检测系统具有图像识别率高、 抗干扰能力强等优点, 因此在许多表面缺陷测领域中被广泛运用。
02螺纹钢表面缺陷分类及成因分析
螺纹钢, 俗称热轧带肋钢筋, 由沿一定长度及方向均匀分布的多个横肋和上下两条纵肋组成。
依据螺纹钢生产企业及相关科研单位的研究统计,常见的螺纹钢表面缺陷类型主要有:气泡、凸块、凹坑、擦伤、麻点等。
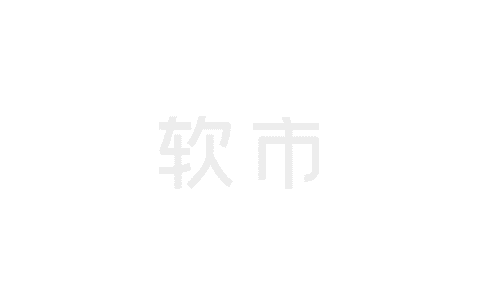
1.气泡
特征:螺纹钢表面皮下气泡产生的无规律点型、 圆形或椭圆形的凸包称之为气泡。未破裂的气泡与烧裂相似, 但其边缘比烧裂光滑, 多产生于螺纹钢的角部及腿尖。
产生原因:
⑴经过多道轧制后钢坯内的皮下气泡或气囊类缺陷没有焊合, 残留在螺纹钢上。
⑵钢坯在炉内烧制过久, 气泡暴露裂开。
2.凸块
特征:螺纹钢表面呈周期性的凸起。小的凸块不影响螺纹钢的使用, 当凸块的高度大于横肋的高度时, 必须检出并报警。
产生原因:
⑴主要是成品孔或者前孔轧槽有砂眼、 掉块或龟裂造成的。
⑵轧制时负荷分配不均导致轧制弹跳变形过大
⑶轧制过程中轧辊材质硬, 撞击轧辊导致轧辊缺肉,造成螺纹钢表面凸起。
3.凹坑
特征:周期性或无规律的分布在螺纹钢表面的大面积块状凹陷。
产生原因:
⑴螺纹钢通过带有凸块的轧辊滚动导板或矫直辊工作面后形成周期性的凹坑。
⑵多余的硬质金属在轧制过程中被压入螺纹钢表面, 脱落后形成凹坑。
⑶由于加热时间过长, 钢坯表面粘附上氧化铁皮, 轧制时压入螺纹钢表面, 氧化铁皮脱落后形成。
4.擦伤
特征:呈直线或者弧形的沟槽, 深度不等, 长度不一, 连续或断续地分布在螺纹钢的局部或表面。
产生原因:
⑴导卫板安装不当, 螺纹钢表面承受压力过大, 轧制时将螺纹钢表面划伤。
⑵导卫板制作工艺不良导致边缘不平滑、 导卫板受损严重或导卫板边缘沾有氧化铁皮, 轧制时将螺纹钢表面划伤。
⑶热轧区辊道、 移钢机或翻钢设备带有尖角, 在运输过程中将螺纹钢擦伤。
5.麻点
特征:表面有大片的凹凸不平的粗糙面, 局部连续或周期性出现在螺纹钢表面。
产生原因:
⑴由于使用时间太久, 轧槽表面磨损严重。
⑵除鳞效果不好, 轧槽上沾有的氧化铁皮被压入螺纹钢表面, 一段时间掉落后形成麻面。
⑶钢坯加热不当、 局部或全部严重脱碳也可能形成麻点。
03基于机器视觉的缺陷检测
工业相机及镜头、 照明光源等硬件是图像采集系统中极为重要的组成部分, 硬件设备的好坏严重影响所采集图像的质量。
工业相机及镜头
相机和镜头是机器视觉系统中不可缺少的构件, 工业相机是视觉成像的主要元器件, 镜头是工业相机用于生成影像的光学部件。
相机部分主要介绍分辨率、 相机类型两个参数。
分辨率:是工业相机的基本参数, 具体由所选择的感光芯片的分辨率决定, 在相同视场成像情况下, 分辨率越高, 拍摄到的细节越多。但过高的分辨率也会占据较大的存储空间。
相机类型:根据感光元件的不同, 工业相机可分为 CCD 相机和 CMOS 相机, CCD相机又可细分为线阵 CCD 和面阵 CCD 两种。CCD 与 CMOS 相机的相同之处在于图像传感器光电转换的原理, 不同之处在于信号的读出过程。
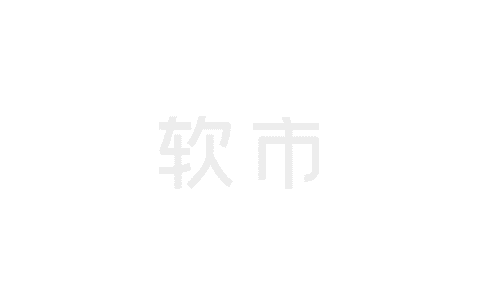
镜头部分主要介绍焦距、 光圈、 景深、 分辨率四个参数。
焦距:镜头的中心到成像面之间的距离叫做焦距。焦距的大小影响了视野范围的大小。焦距越短, 视野范围越大, 焦距越长, 视野范围越小。
光圈:常位于镜头内, 用于控制光线经过镜头进入机身内的通光量。焦距越短,光圈越大, 焦距越长, 光圈越小。
景深:在一定距离内拍摄物体, 能够形成清晰影像的物距范围叫做景深。距离物体近时, 景深小, 距离物体远时, 景深大。
分辨率:镜头的分辨率是指在像平面处 1 毫米内能分辨开的黑白相间的线条对数。光圈越大, 景深越小, 分辨率越高, 物体成像越清晰。
光源在缺陷照明系统中起着十分重要的作用, 机器视觉检测应用中照明装置常用的光源为 LED 光源、 卤素灯和荧光灯等。
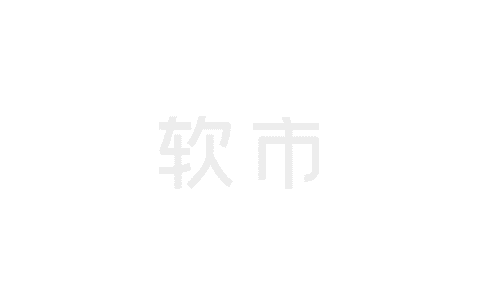
软件组成
国内做机器视觉系统的有很多,如何选择成为头疼的问题,今天重点为大家讲述选择机器视觉软件的几个关键点。
机器视觉软件选型要点
1、图像预处理
大部分的图像处理软件提供预处理算法,所以需要比较其提供的丰富程度,效率等。
2、易于编程和操作
简单直观的图形界面是易于使用和设置的关键。当今机器视觉产品的主要区别在于它们的图形界面。界面应根据“设置”和“操作”进行评估。
3、便于升级
当挑选一个机器视觉软件时应思考系统将来的升级问题。
矩视智能是一家致力为自动化系统集成商及其工程师团队赋能,提供机器视觉低代码开发平台,坚持“0代码、0门槛、0硬件、0成本”的产品理念,全面提升机器视觉开发供给能力,推动机器视觉普惠化落地。
与其他提供定制化服务的视觉解决方案商不同,矩视智能提供标准化的机器视觉低代码协同开发平台。目前矩视拥有开发者工具平台形式的SaaS和aPaaS系列产品。
将传统PC-Based的软件形态,升级为云端SaaS形态,从而在行业内大范围积累数据,并运用数据让产品更加“傻瓜化”,方便工程师使用;由于采用PLG的增长模式,矩视选择面向视觉、软件、电气、结构等工程师,免费授权使用开发环节,进一步降低机器视觉的使用门槛,以此良性循环,扩大产品的使用人群。
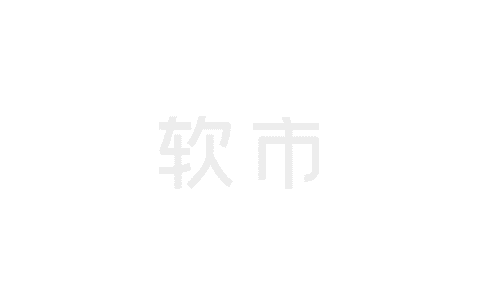
该方法可靠性高、 可扩展性强,不仅降低了螺纹钢缺陷的漏检率和废品率, 还解决了生产现场环境恶劣、 工人操作危险和实时性差等问题。
矩视智能机器视觉低代码平台是一个面向机器视觉应用的云端协同开发平台,始终秉承0成本、0代码、0门槛、0硬件的产品理念。
平台以人工智能技术为核心,在机器视觉应用开发环节,为开发者提供图像采集、图像标注、算法开发、算法封装和应用集成的一站式完整工具链。覆盖字符识别、缺陷检测、目标定位、尺寸测量、3D测量、视频开发等上百项通用功能,致力于成为全球用户量最多,落地场景最广泛的机器视觉低代码平台。
更多功能正在开发中,最新信息会第一时间在官方公众号“矩视智能”进行公布,大家持续关注哦!
来源:矩视智能
声明:本站部分文章及图片转载于互联网,内容版权归原作者所有,如本站任何资料有侵权请您尽早请联系jinwei@zod.com.cn进行处理,非常感谢!